以数字化双碳技术赋能工厂
打造绿色工厂,助力企业零碳转型
应用场景
制造工厂
化工工厂
加工工厂
电子工厂
食品加工厂
物流工厂
客户痛点
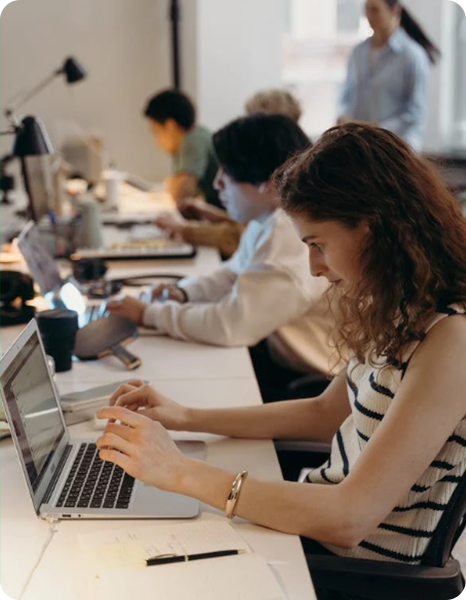
信息化管理水平低
信息化管理水平低
管理粗放,人工管理,效率低。
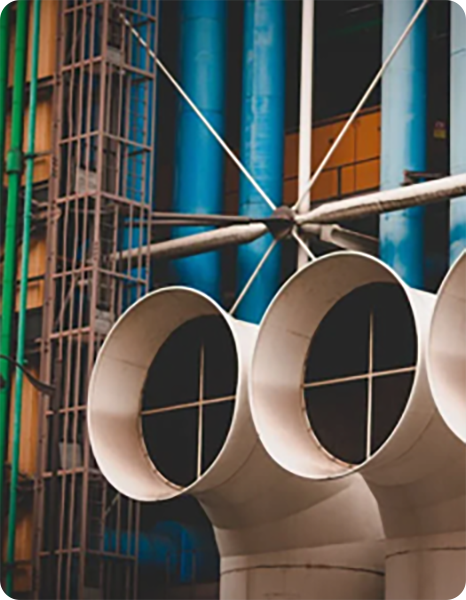
工厂用能成本高
工厂用能成本高
耗能高,经营成本较大,管理难度大。
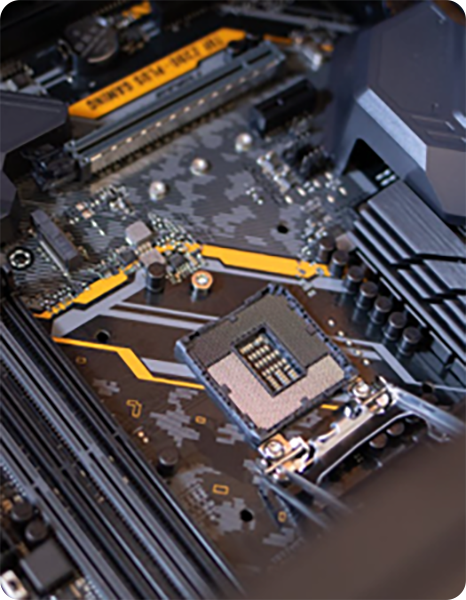
缺少数字化预测服务
缺少数字化预测服务
无法提前预测设备健康情况,设备故障可能导致能源浪费和生产中断。
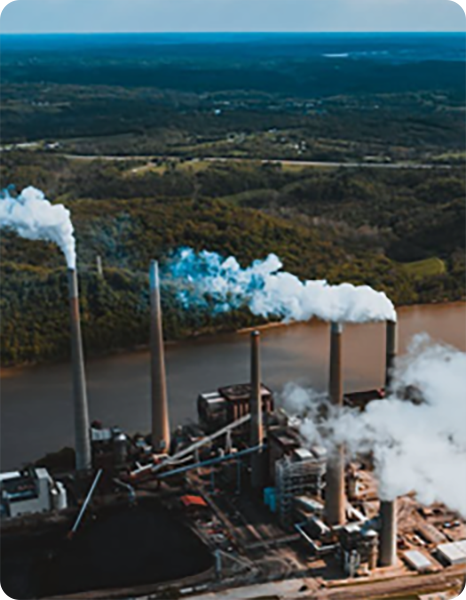
碳管理方法不清晰
碳管理方法不清晰
碳排放量无法准确跟踪计算,无法满足碳排要求,可能带来经济损失。
解决方案
厘清产品碳足迹,顺应绿色贸易需求,助力企业打造低碳生产链
物联网IOT部署传感器和物联网设备收集工厂内各个环节的实时能源数据,追踪设备状态,生产能效和能源使用情况,提供数据基础支持。
数字孪生利用数字孪生技术,将实际工厂的物理过程数字化,模拟并优化生产和能源流程,预警设备信息,降低能源消耗并提高效率。
虚拟电厂将工厂连接到智能电网,通过虚拟电厂平台整合分布式能源资源,优化能源生产和分配,提高能源利用效率。
碳排管理碳咨询服务、碳排放监测、碳排放核算、多维度碳排分析全生命周期一站式碳管理服务,帮助用户降碳增效。
应用案例
资源共享与业务协同,零碳生产就在我们身边
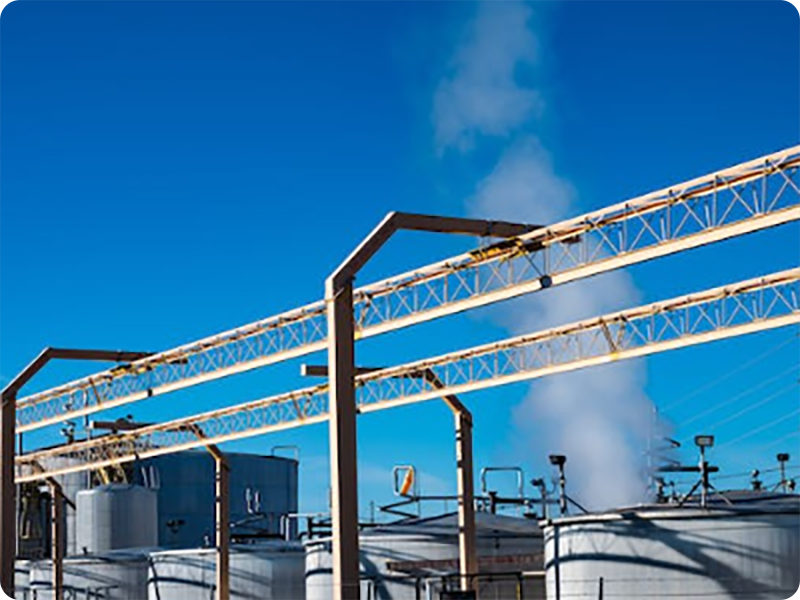
江苏盐城某零碳工厂
项目情况
工厂位于江苏盐城,主要生产工业配件,历史年用电量约440万kWh,工厂未接入光伏发电,工厂内部能源管理信息化水平低,设备数据无法自动采集,手工抄表工作量大,厂区异常情况无法预警。
方案情况
以软件+硬件+增值服务的模式为用户打造零碳工厂场景,工厂屋顶安装2.78MW光伏,由零碳平台提供数据的采集、数据分析和上层应用。提供“双碳”战略咨询增值服务,包含制定脱碳路线图、碳排计算,提供电力交易服务以及虚拟电厂响应服务,低成本实现外购电力需求;同时还提供绿电、绿证及碳信用采购服务,助力工厂实现零碳运营。通过代理电力交易节约电费2万元/年,年节省绿电采购费用5.56元/年。
天合光能常州零碳工厂
项目情况
天合光能常州工厂占地面积15万平方米。分为西区、东南区、东北区三个厂区,是天合光能产品研究、开发和制造总部基地。全厂能源消耗量大,全年有冷水需求,冬季有供热需求,随着天合光能打造多能互补、智能高效、绿色低碳的现代工厂能源体系,原有的能源使用模式不再符合公司战略要求。
方案情况
在东南厂区,结合工厂用电、用冷、用热需求,整合燃气分布式、水蓄冷、储能,通过零碳平台能源管理系统对东南区负荷进行实时监控、有效调节,通过节能管理、改造,优化调整电源结构,提升了能源价值、降低了用能成本、增强了供能灵活性和安全性,建立了清洁高效的能源体系。项目实施符合国家的产业政策,符合天合光能战略转型需要,对区域社会、经济、环境均具有积极作用。
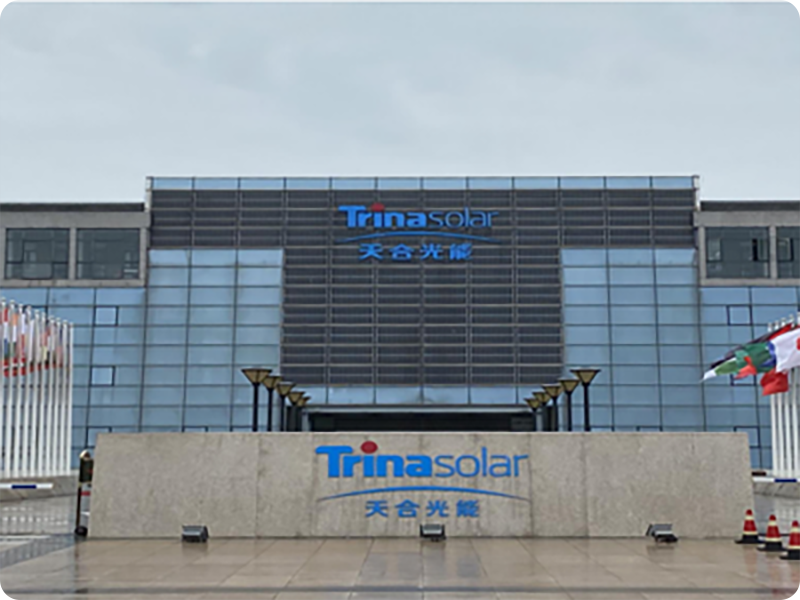